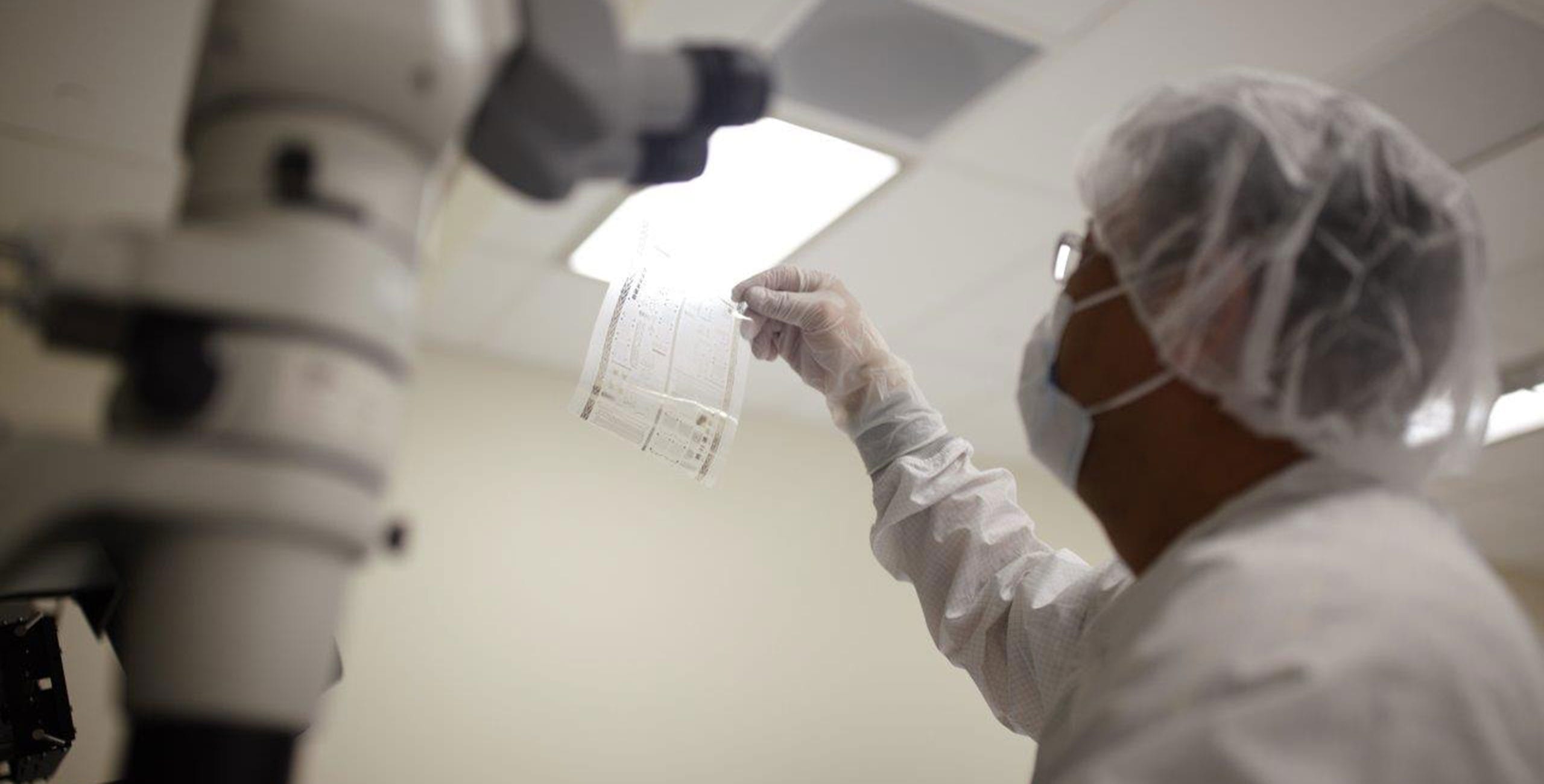
An Interview with Ethan Secor, Assistant Professor of Mechanical Engineering at Iowa State University
Question: Ethan, can you tell us a little about your role at Iowa State University and the focus of your organization?
Answer: I am an Assistant Professor at Iowa State University, a land-grant research university with a mission that spans research and education. We actively work to prepare undergraduate and graduate students for the future workforce and pursue fundamental science and engineering with broad impact.
Q: Iowa State University is a newer member of NextFlex. What drew you to the FHE manufacturing community and what are you hoping to accomplish through your membership?
A: As an academic institution, NextFlex offers an ideal ecosystem to connect fundamental research with industry and government stakeholders. Through participation in NextFlex, we gain practical insight on technology needs and trends to better tailor our broad research for long-term impact. Moreover, this membership provides our students and graduates with avenues to transition into industry positions with better awareness of the technology landscape and major stakeholders. While we traditionally work on low-TRL/low-MRL projects, participation in NextFlex provides a broader perspective to ensure that successful low-TRL projects have a clear runway and strong demand to pull them forward for ultimate use.
Q: What is a key innovation that will enable widespread adoption of FHE and related technologies, and what application areas are you working in?
A: In my mind, the digital nature of many advanced manufacturing technologies provides a viable opportunity for improved integration of computational tools. Ultimately, realization of this potential by collecting more/better data from the process and coupling this with robust computational methods, will support improved automation to drive adoption of FHE technologies. Our work in this space has primarily been focused on a single FHE technology, aerosol jet printing, for which we aim to improve in situ diagnostics for process monitoring and control.
Q: What upcoming activities are you most excited about?
A: The proximate cause for our involvement in NextFlex is an upcoming project funded through PC8.6 that is focused on process monitoring and control for aerosol jet printing. It’s a technology that we have been working on for several years, and we are excited to work with Optomec, Inc. to validate this technology for commercial printing equipment. We believe it has strong potential to improve reliability for hybrid electronics manufacturing and provide real-time data to support better digital integration of the fabrication system. NextFlex helped connect us to industry engineers to develop this project, and this support provides a great opportunity for us to work with Optomec, Inc. to move our technology towards practical application.
Q: In what ways do you think NextFlex and flexible and hybrid electronics can impact microelectronics manufacturing and / or your own product development?
A: I think the FHE ecosystem supported by NextFlex has an important role in advanced packaging for microelectronics. The versatility of digital manufacturing tools can support more decentralized operations, which can accelerate innovation in microelectronics applications by allowing a wider variety of stakeholders to develop custom solutions.