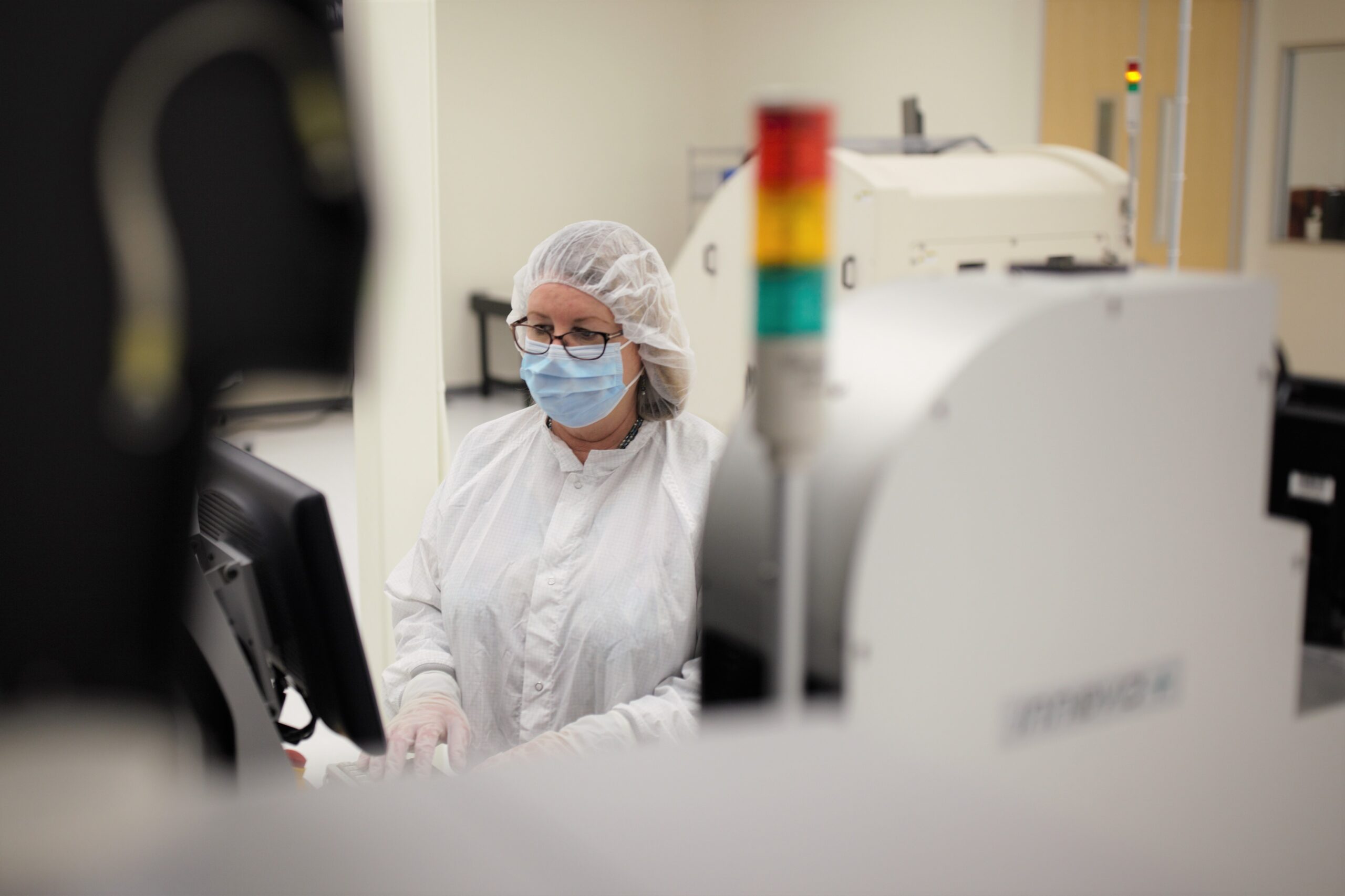
NextFlex News – December 2021
Dear Colleagues and Friends,
As 2021 draws to a close, I take this moment to appreciate the progress that we’ve made together and the tremendous support we’ve received from members, government partners and the FHE community at large. Creating a strong industrial manufacturing base in the US for flexible hybrid electronics is core to our mission, and the depth and quality of the funded projects now underway show that the technology is advancing and that FHE-enabled products are moving through the pipeline to commercial availability. I was pleased to be able to share the impact we are having with colleagues at the Defense Manufacturing Conference this week in Denver.
Along with Executive Directors from the other eight DoD institutes, I presented NextFlex results to date as part of a panel entitled, “A DoD Mission and A National Imperative.” It was an eye-opening session. Hearing about advancements in each of the institutes’ respective technology focus areas was energizing, and we came away with new ideas about how to accelerate our progress even further.
The strength of the NextFlex manufacturing consortium brings together diverse and collaborative subject matter experts for projects and technical working groups, and because the member community is well established, we can be agile in engaging technology-adjacent groups as a mechanism for solving problems in related technology areas. Examples of progress in this area are the addition of an automotive-focused technical working group, development of methods for integrating FHE into future roadmaps for packaging integration, and project collaboration with sister DoD institutes AFFOA and ARM.
The NextFlex Technology Hub has made great strides in supporting the DoD and our members with new tools and processes that enable additive manufacturing for novel electronics and heterogenous integration, as well as for multilayer and embedded components. We now routinely support both commercial and DoD customers with design, prototype, and pilot scale production of devices and systems. We’re gathering and reporting data focused on reliability and have added capability for firmware and software programming.
The area that has seen enormous growth this year is in our workforce development programs as we work to secure the human capital needed for advanced manufacturing in the future. We now have 14 active ecosystems around the country in seven states and have increased our number of industry partners to 47. These partners, along with our stellar community college partners, have helped us to reach a total of 7,000 students since the launch FlexFactor®, our project-based learning program for high school students, at the end of 2016. This is astonishing progress, and we just keep going, adding new programs that support college Learn and Earn programs as well as leading the development of digital courses to help product developers take advantage of the benefits of FHE – lower cost, lower weight, thin and conformal form factors, high mix, low volume production, all attributes that were previously not viable with traditional board/system manufacturing processes.
The future is bright for flexible hybrid electronics. The technology paves the way for higher levels of integration previously not possible and provides an opportunity for US leadership as we create new form factors and manufacturing approaches that eliminate the distinction between package, PCB, and system. It’s an exciting time and I encourage you to get involved, stay involved, and lend your support and good ideas as we move into the new year.
I wish you all the best this holiday season and I thank you again for your support, encouragement, and ideas.
Sincerely,
Malcolm J. Thompson, PhD